Facilitating World Class Research
FloWave: Making Waves in the Energy Sector
Prototype tidal and wave energy converters must make their first trip to the sea with confidence. Once proven in commercial operation, they perform to expectation in terms of lifetime energy production and durability. Early and unforeseen failure can is avoidable by extensive and sufficient numerical modelling combined with scaled physical testing. Unsuccessful operations at sea are financially (and reputationally) damaging for developers and the fledgeling ocean renewable energy (ORE) sector at large. It is cheaper and safer to learn as much as possible, including from mistakes, by repeatedly testing indefinable and controlled conditions on dry land, but that is as close as possible to those in the open sea.
The open sea is the most arduous immediate and long term environment within which tidal, wave and floating wind technologies must expect. Complex waves and highly turbulent tidal currents arrive in independent, multiple and varying directions to combine and act on all of these technologies. They even combine to influence the raw power quality of the electricity generated. To approach, at scale, the conditions in most locations worldwide, ERM staff designed and built the FloWave Ocean Energy Research Facility.
It is the world's first circular combined wave and current test basin, 25 m in diameter with a test depth of 2m above its rising, created with support from the Engineering and Physical Sciences Research Council, Scottish Government. It contains 2400 cubic metres of water surrounded circumferentially by 168 absorbing wave-makers.
The force-feedback paddles preserve the complex spectral and multi-directional wave climate created with waves up to 0.7 m in height (scaled up this is 28 m in the actual sea). FloWave's control system can rotate the wave activity's incident direction to replicate the sea's variable storm conditions. They can create complex, repeatable tidal flow emulations at up to 1.6 metres/second in any direction across the tank, even curving in full 360-degree rotation in either direction to approach the varying ebb and flow patterns of tidal currents (up to 12 knots) in real-life channels.
With dedicated technical staff, a fully equipped workshop enables the manufacture of components to support clients' scale models' preparation and testing. The industrial and academic developer community utilises FloWave to test over 40 commercial technologies for wave, tidal, and offshore wind energy conversion. The facility and its staff have been a critical strategic component in the Wave Energy Scotland (WES) Novel Wave Energy Converter (NWEC) programme.
FASTBLADE Structural Composites Research Facility
Accelerated Lifetime Testing
The innovative structural composites research facility has been developed by the University of Edinburgh specifically for cost effective, accelerated testing of stiff and slender composite and metal structures, such as tidal turbine blades, composite bridge sections and carbon fibre aircraft wing boxes. The facility will be the first of its kind in the world and will use a Digital Displacement® regenerative hydraulic actuation system to reduce the energy requirements of fatigue testing.
Rapid Evaluation and Reduced Design Risk
FASTBLADE will reduce design risks for developers by providing the opportunity for more and better data sets, thanks to reduced product testing time. This will enable more and faster impact-led academic research into fundamental engineering options for new, advanced materials. The accelerated evaluation of specimens will enable the more rapid evaluation, certification and deployment of new products to market.
Supporting the Tidal Energy Sector
FASTBLADE will help secure Scotland’s lead in marine energy as the world’s first dedicated fatigue test facility for tidal blades. The project exemplifies the University of Edinburgh’s Leadership in Research on an industrial site. The industrially focused facility was developed ‘for industry & with industry’. FASTBLADE will deliver new jobs and attract businesses to Scotland for composites products and tidal blade development. The team are already scoping new training programs and apprenticeships focused on data collection in an industrial setting for an authentic experience.
This innovative Structural Composites Research Facility (SCRF) is aimed primarily at accelerated lifetime testing of composite tidal turbine blades. Since the project’s conception, the tidal energy sector has successfully grown and now requires a facility capable of testing larger and stiffer blades than anticipated.
Working with Babcock Marine Limited to develop the FASTBLADE facility at the Rosyth Dockyard in Fife, the site was developed for faster fatigue or cyclic load testing of large structures. This was initially focussed on fibre-reinforced composite material structures, such as stiff tidal turbine blades (e.g. fabricated from carbon fibre and glass fibre reinforced polymer resins).
The facility is the first of its kind in the world, using a brand new, ultra-efficient digital displacement regenerative pumping hydraulic system. For fatigue testing of tidal turbine blades, the novel hydraulic actuation system uses only use 25% of the energy input required by conventional hydraulic testing systems, and will test structures 8 times faster than possible with existing hydraulic systems (test frequency increase from 0.1 Hz to 1 Hz).
This will enable more and faster impact-led academic research into fundamental engineering options for new materials technology and accelerated evaluation of tidal turbine blades leading to more rapid certification and deployment to market. Such a capability is critical to the success of this emerging composite materials technology for renewable energy and will accelerate the conversion of available tidal marine energy, which is currently under-exploited at a time of increasing national demand for energy.
Nationally, the facility underpins fundamental research in composite materials across all sectors, to be targeted at applications in high value manufacturing sectors such as aerospace, automotive, and civil engineering applications (e.g. structural health monitoring in bridges and buildings subject to ongoing fatigue under cyclic loading). Academics will benefit by access to a state-of-the art accelerated fatigue testing facility, opening new research opportunities on fundamental materials and process topics.
Industry will benefit by reduced design risk from better testing data and by reduction of product testing time, within the product development cycle times needed in the renewable energy, aerospace, naval defence, marine and infrastructure sectors.
The £3.7M Medical Device Manufacturing Centre (MDMC) is jointly funded by the European Regional Development Fund managed by Scottish Enterprise, the Edinburgh & South East Scotland City Region Deal, and the universities.
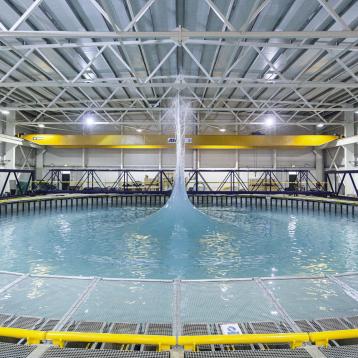
Flowave concentric wave spike
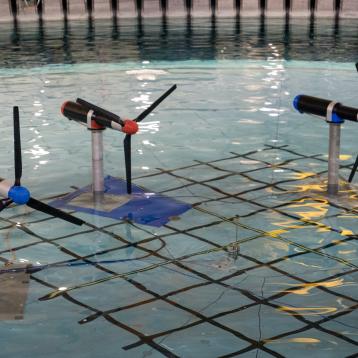
Commercial tidal wave testing
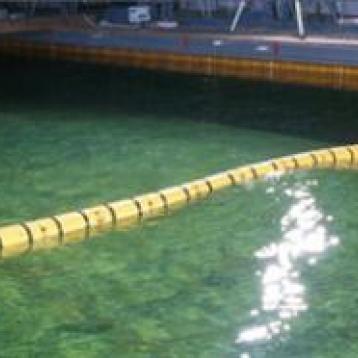
Scale model testing
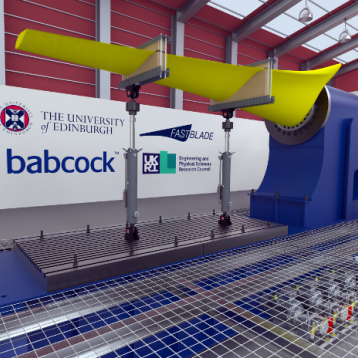
Fast Blade Simualtion
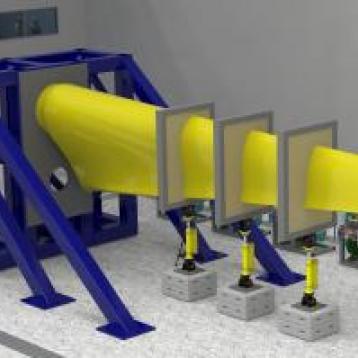
Fast Blade Graphic